Conformal coating is utilized to safeguard the components on a printed circuit board against environmental factors such as moisture, dust, salt, and chemicals. To apply this coating, it’s crucial that the printed circuit board supports it.
Surface energy vs. surface tension
Surface chemistry is an extremely complex and challenging branch of science. You refer to surface energy in solids, while in liquids, you speak of surface tension. In practice, these terms are often used interchangeably.
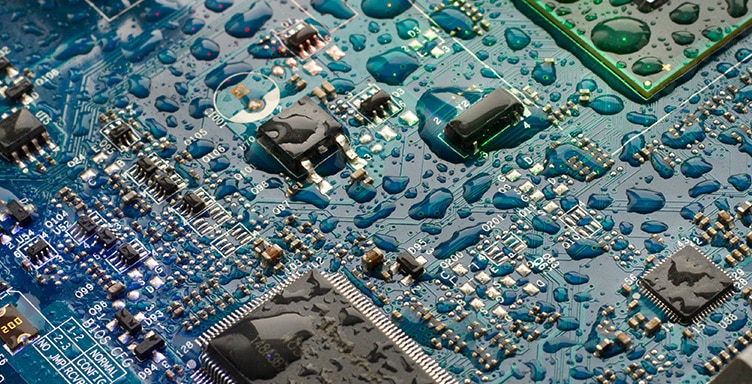
Printed circuit boards & surface energy
The surface energy of solids is typically expressed in dynes per centimeter. We abbreviate this to ‘dynes’. The surface energy of a printed circuit board is generally determined by the solder mask. A common value is, for example, 36 dynes.
Inspection of printed circuit boards
To measure the surface energy of a printed circuit board, a line is often drawn on the board using a dyne pen. These pens contain a solution with a predetermined surface tension. If the surface energy needs to be 36 dynes, a corresponding pen is used to draw a line on a sample.
If this line forms a sharp edge without spreading on the print, the solder mask meets the specified surface energy.
How many dynes is sufficient?
It is important to discuss this with the supplier of the conformal coating. They know the required surface energy for the printed circuit board.